Solvent Recovery Unit (SRU)
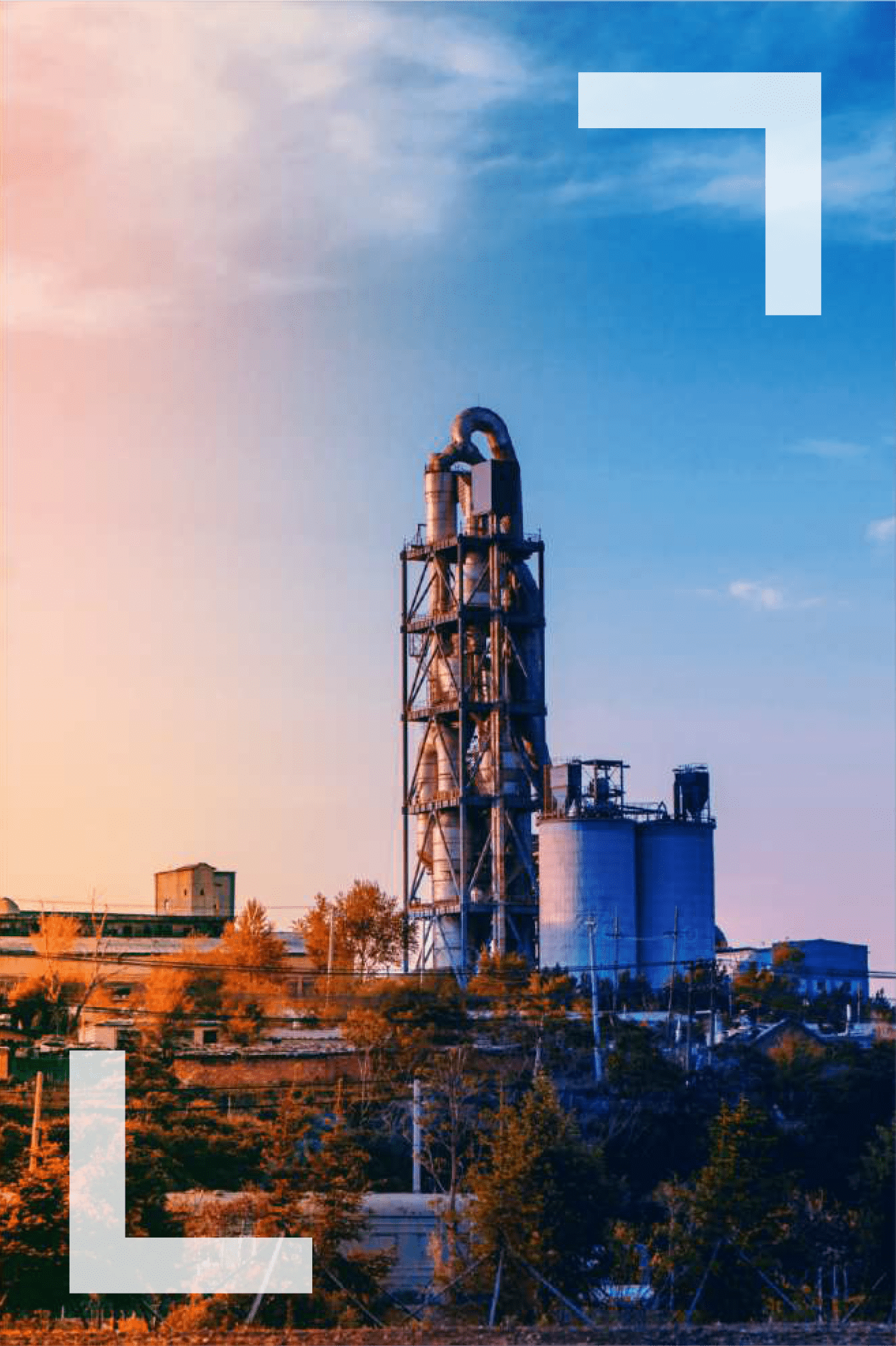
Introduction of Solvent Recovery Unit
Pexomass in India offers perfect solutions in the field of Solvent Recovery. So you get the benefit of established technological expertise and Pexomass's proven engineering skills.
Pexomass is a recognized leader in the fields of vapor phase solvent adsorption using activated carbon and solvent recovery. It has over years of worldwide experience, and with thousands of systems in operation, helps companies recover millions of kilos of solvent/VOCs each year.
Known for its conservative engineering, quality equipment and services, and seasoned team of engineers, Pexomass provides design, engineering, equipment and installation of recovery systems, using activated carbon or zeolite adsorbents for solvent recovery and VOC emission control.
Pexomass plants are high-performance, cost-efficient process systems that meet each client’s individual requirements.
Pexomass is a well-known company that offers a variety of technologies and machines to various industrial segments. Our highly qualified team of trained engineers and partnerships with global leaders enable us to provide cutting-edge solutions to the industry. Continuous innovation and advancement have been a hallmark of Pexomass.
Our workshop near Mumbai is 5000 sq. m. large and has a workforce with a cumulative experience of over 1000 man years.
At Pexomassl, we don’t sell machines, we provide solutions. Once you are a Pexomass customer, we are completely at your service. So whether it’s a spare part you need or an entirely new machine, we are always there for you.
Solvent Recovery Unit (SRU)
A solvent recovery unit, also known as a solvent recovery system or solvent recycling unit, is a piece of industrial equipment designed to recover and reuse solvents that are used in various manufacturing processes. Solvents are often used to dissolve, disperse, or extract substances in industries such as pharmaceuticals, chemicals, paints, coatings, & electronics manufacturing. However, solvents can be expensive to purchase and dispose of, and their improper handling can lead to environmental and health concerns.
A solvent recovery unit works by distilling and separating the solvent from the contaminants, impurities, and residues it has picked up during the manufacturing process. Here's how a typical solvent recovery process might work
- Collection : The used solvent, which may contain dissolved materials, is collected from the manufacturing process. This solvent is often referred to as "dirty" solvent.
- Distillation : The collected dirty solvent is heated in a distillation chamber. Solvents have lower boiling points than many of the contaminants they may have picked up during use. As the solvent vaporizes, it rises and is collected in a separate chamber.
- Separation : The vaporized solvent is condensed back into a liquid state by cooling it down. Since the contaminants have higher boiling points, they are left behind in the distillation chamber. This separation process helps to purify the solvent.
- Recovery : The purified solvent is then collected and can be reused in the manufacturing process. The recovered solvent is often referred to as "clean" solvent.
Benefits of Using a Solvent Recovery Unit Include
Cost Savings : Recycling and reusing solvents can significantly reduce the need to purchase new solvents, leading to cost savings.
Environmental Impact : Proper solvent recovery helps reduce the amount of hazardous waste generated and decreases the overall environmental impact of the manufacturing process.
Regulatory Compliance : Many industries have regulations and guidelines for the proper handling and disposal of solvents. Using a solvent recovery unit can help companies stay compliant with these regulations.
Resource Efficiency :By reusing solvents, companies can conserve natural resources used in solvent production.
Improved Sustainability :Solvent recovery is part of a more sustainable approach to manufacturing, which is becoming increasingly important for companies looking to improve their environmental footprint.
Plant Process Hierarchy
Dirty Solvent > Distillation Chamber > Condensation Chamber > Clean Solvent
It's important to note that different industries and processes may require specific solvent recovery units tailored to their needs. The design and capacity of these units can vary based on factors such as the type of solvents used, the volume of solvent waste generated, and the level of purification required.
Pexomass's offers
International cutting-edge technological solutions that are the most advanced in Asia. Customized creative and economical development of machines and auxiliaries Prepurchase counseling, validation through trials, and service needs Superior process know-how, speedy execution, and exemplary after-sales service.
How Pexomass Works in the Solvent Recovery Unit Manufacturing
Pexomassl Solvent Recovery Plants are designed and constructed to the highest engineering standards and offer guaranteed performance. They provide continuous 24/7 automatically controlled operations both for large specially engineered installations or packaged units requiring only to be set down and connected to services. Pexomass can recover solvent with up to 97% efficiency and eliminate air pollution hazards at the same time. The purity of the returned solvent is guaranteed.
Pexomassl also offers a complete engineering service including detailed surveys for the evaluations of the economics involved in recovery and reuse of your solvent.
Solvent Recovery Process
The Solvent Laden Air (SLA) is conditioned (filtered and treated for temperature and humidity) prior to adsorption by passing it through the SLA Cooler (2) and SLA Re-Heater (3).
Recovery begins when the SLA Fan (4) passes the SLA through Adsorbers (5) of packed beds of activated carbon. The solvents are retained in the activated carbon pores and the cleansed air is discharged into the atmosphere.
Through staggered adsorption and desorption cycles monitored by analyzers and computers, each bed is periodically regenerated by a counter flow of steam or inert gas that heats the carbon.
During the regeneration phase, the solvent vapors are released from the carbon and carried by steam or inert gas to condensation (6), decanting, and solvent treatment units.
Solvent treatment systems are custom-designed to meet each client’s requirements. Decanters (11) are used for separation of solvents that are nonmiscible in water. Other cost-effective processes and equipment include air stripping, steam stripping, and steam distillation.
Additionally the recovery efficiency can be improved by providing a Drying and Cooling unit (8,9, 10) after the regeneration before the next adsorption cycle.
Benefits of Solvent Recovery Unit
Suitable for a range of air flows, variety of solvent types, and solvent loadings Very high emission control and recovery efficiencies of 95% and above.
Fully automated systems including PLC operations result in minimal manpower to operate the plant following full safety precautions.
Reuse of solvent reduces manufacturing costs resulting in attractive Pay Back Periods of about 2 years.
Packed bed Activated Carbon Solvent Recovery Plant helps comply with environmental pollution control.
Helps combat global warming by recycling and reuse of natural resources.