Agitated Nutsche Filter Dryer ( ANF / ANFD )

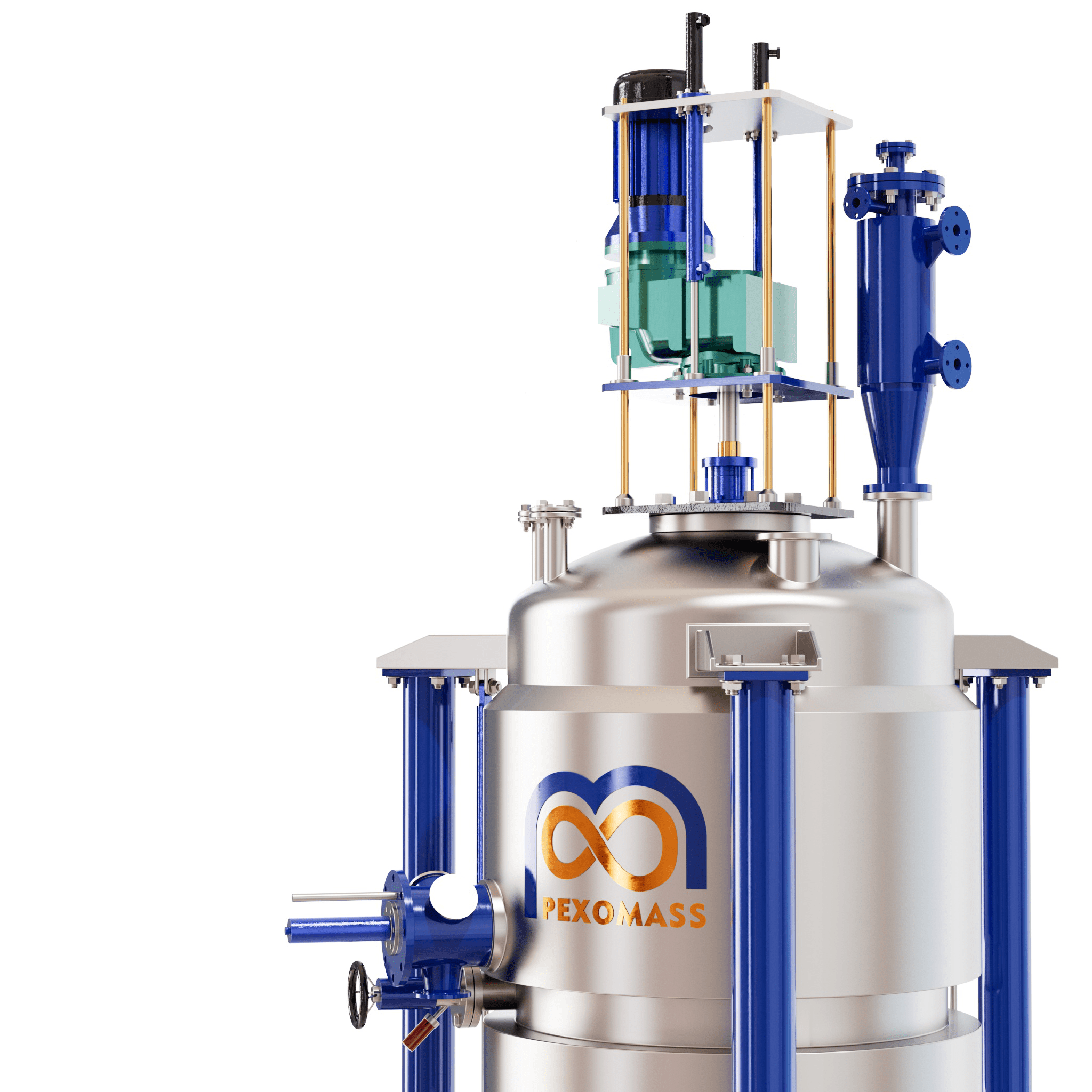
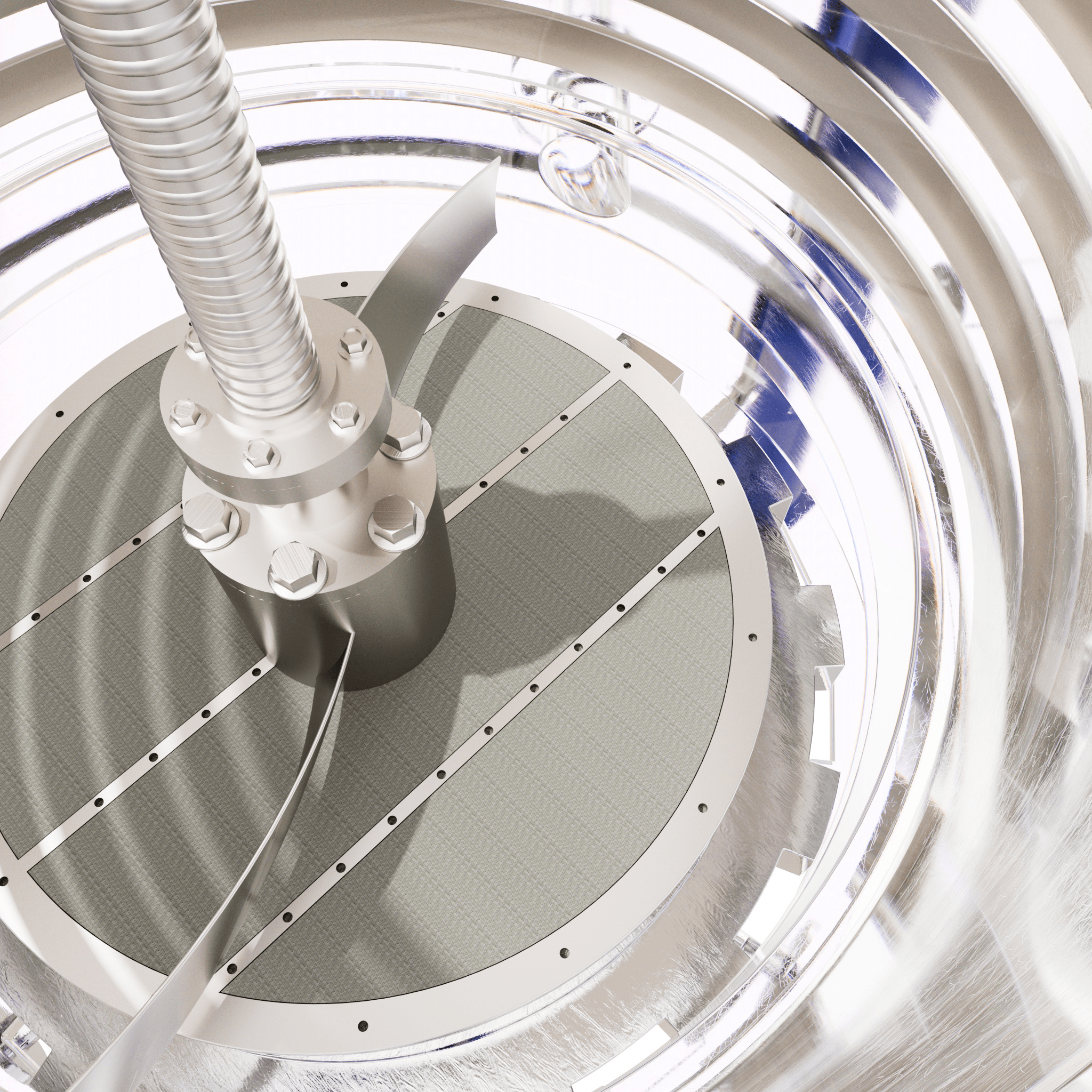
Agitated Nutsche Filter Dryer ( ANF / ANFD )
ANFD stands for "Agitated Nutsche Filter Dryer." It is a specialized equipment used in the pharmaceutical, chemical, and fine chemical industries for solid-liquid separation, filtration, washing, and drying of solid materials in a single process vessel. ANFD combines the functions of a filter, agitator, and dryer into a single unit, making it a versatile piece of equipment for various processes.
Working Principle
The ANFD consists of a cylindrical vessel with a filter plate and a filter medium (often a filter cloth) covering the perforations. This allows the liquid component of the slurry to be separated from the solid material. The slurry containing the solid material and the liquid is fed into the vessel. The liquid passes through the filter medium and the perforations, leaving the solid material behind on the filter cloth.
If necessary, the solid material can be washed to remove any impurities or unwanted components. The washing liquid is introduced into the vessel and agitated to ensure thorough contact with the solids.
The vessel is equipped with an agitator (usually a paddle or a ribbon) that rotates and agitates the contents. Agitation prevents the formation of a compact cake on the filter medium and aids in uniform drying.
After the filtration and, if applicable, washing stages, the drying process begins. The vessel is heated, and the agitator continues to rotate, ensuring that the solid cake is exposed to heat & air. As the vessel is heated, the moisture in the solid cake evaporates, and the solid material gradually dries. The agitator prevents the cake from sticking to the filter medium and ensures even drying.
Once the drying process is complete, the dried solid cake can be discharged from the vessel. The agitator can aid in breaking up the cake, making it easier to remove.
: After the process is finished, the ANFD is cleaned to prepare it for the next batch. This involves removing any remaining material from the vessel, filter medium, and agitator.
Components of ANFD
Advantages of ANFD
Combining multiple process steps (filtration, washing, and drying) in a single vessel reduces the need for transferring materials between different equipment, leading to better process efficiency.
It saves by reducing the need for separate equipment & minimizing material handling.
As the entire process takes place within a closed vessel, it reduces the risk of product contamination and exposure to environments.
By containing potentially hazardous or toxic materials within the closed vessel, ANFDs enhance operator safety
The advantages include efficient filtration, washing, and drying in a single unit, minimizing the need for multiple pieces of equipment and reducing processing time. It's particularly useful for heat-sensitive materials or processes that require maintaining product quality. ANFDs find applications in various industries, such as pharmaceuticals, chemicals, dyes, pigments, food processing, and more, where the separation, washing, and drying of solid materials are essential steps in the production process